GLT-01 בודק בועות דליפות גסות
- תֶקֶן: ASTM F2096
- יַצרָן: מכשירי תא
- יישומים: חומרי אריזה, חומרי מכשור רפואי, בדיקות פרמצבטיות, דבקים, טקסטיל, מיכלי נייר וקרטון ועוד.
- התאמה אישית: זמין עבור דרישות בדיקה מיוחדות וטרנספורמציות אוטומציה
I. מבוא לבוחן בועות דליפות גסות
In quality assurance of sterile and sealed packaging, detecting large breaches that compromise product integrity is crucial. The gross leak bubble tester is a highly effective, visual inspection method for identifying such defects. Commonly used in industries like food, pharmaceuticals, and medical device packaging, this method helps verify seal strength and barrier integrity before products reach the end user.
The test follows a simple principle: by immersing the package in water and applying internal air pressure, visible bubbles will form if a leak exists. This intuitive approach, standardized by ASTM F2096, makes gross leak detection both accessible and highly accurate.
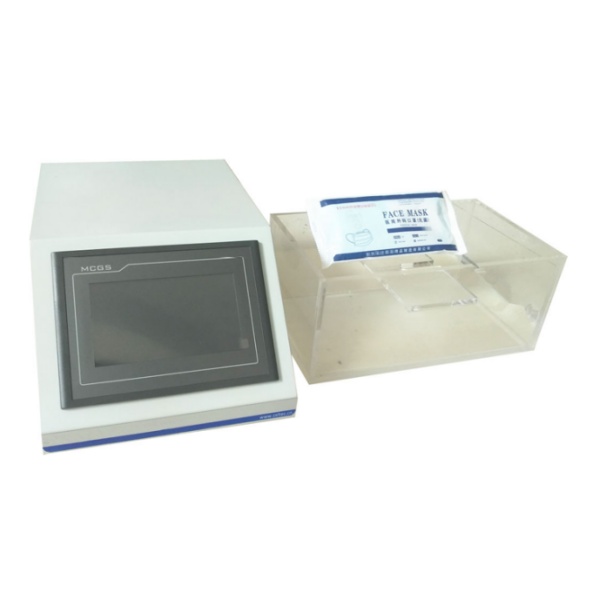
II. How Gross Leak Bubble Testers Work
א gross leak bubble tester uses a pressurized air system and a water-filled chamber to visually detect large leaks in packaging. Here’s a breakdown of the testing procedure:
- Package Puncturing: A controlled puncture allows insertion of an air line and pressure gauge.
- Submersion: The test sample is submerged 25 mm (1 in.) underwater in a transparent chamber.
- Pressurization: Air is introduced gradually until the desired pressure is reached.
- Observation: If a leak is present, a continuous stream of bubbles will emerge from the compromised area.
ה bubble leak testing method offers high sensitivity and quick visual confirmation, making it suitable for quality control across diverse packaging formats like pouches, trays, and foil-sealed containers.
III. GLT-01 Gross Leak Tester by Cell Instruments
To meet the growing demand for reliable, easy-to-operate leak detection equipment, מכשירי תא offers the GLT-01 Gross Leak Tester. Designed in strict accordance with ASTM F2096, this tester is suitable for a wide range of packaging types and supports both bubble test and optional pressure decay methods.
Key Features of the GLT-01 Include:
- מערכת בקרת PLC with intuitive touch-screen interface
- Stable gas supply ensuring consistent pressurization
- Transparent acrylic chamber for unobstructed observation
- אופציונלי integration with pressure decay method for expanded test capabilities
With a testing range of 0–30 KPa and a chamber size of 34×20×15 cm, the GLT-01 is ideal for labs and production facilities needing dependable and repeatable gross leak testing results.
IV. ASTM F2096 and Bubble Leak Testing
ASTM F2096, titled “Standard Test Method for Detecting Gross Leaks in Packaging by Internal Pressurization (Bubble Test)”, outlines how to use internal pressurization to expose seal defects. This method is widely referred to as the bubble leak test אוֹ gross leak test. It is destructive and suitable for both porous and nonporous packaging materials.
Key highlights of ASTM F2096 include:
- Test sensitivity down to 250 μm at an 81% probability.
- Differentiated procedures for porous vs. nonporous packages.
- Emphasis on establishing the appropriate test pressure for reliable results.
- Testing is especially valuable when package dimensions do not conform to other integrity test equipment.
This method is not only practical but also cost-effective for manufacturers and quality labs seeking robust leak detection protocols.
V. Applications of Gross Leak Detection
Industries where sterility and contamination prevention are critical rely heavily on gross leak detection:
- Medical device packaging (e.g., syringes, catheters)
- תרופות (e.g., blister packs, sterile barrier systems)
- Food packaging (e.g., vacuum-sealed pouches, retort bags)
- Consumer goods requiring seal assurance (e.g., cosmetics, hygiene products)
The test is particularly valuable when products must comply with regulatory guidelines for barrier performance and microbial ingress prevention.
VI. Why Choose Bubble Leak Testing?
There are many methods available for package integrity testing, but the gross leak bubble tester remains a preferred solution due to several advantages:
- Simplicity: No complex instrumentation is required beyond air pressure control and a water bath.
- Visual confirmation: Bubbles make leak location immediately visible.
- רבגוניות: Accommodates both large and small packages.
- Low cost: Ideal for routine inspections without high overhead.
Most importantly, bubble leak testing directly ties into consumer safety and regulatory compliance, especially for sterile medical and food applications.
VII. Best Practices for Bubble Leak Test Setup
To ensure accurate and repeatable results, follow these best practices:
- Use fixtures to maintain consistent package positioning.
- Maintain test pressure in accordance with ASTM F2096 Appendix A1.
- Rotate the package during inspection to check all surfaces.
- Avoid over-pressurization, which could damage seals and cause false positives.
- Use a chamber with transparent walls to improve visibility.
Proper training and consistent procedure execution will maximize test reliability.
שאלות נפוצות
It is suitable for a wide variety of flexible and semi-rigid packaging including pouches, trays, foil wraps, and sterile barrier systems.
ASTM F2096 identifies gross leaks as those large enough to be visually observed through a continuous stream of bubbles under defined pressurization conditions.
Yes, the method involves puncturing the package, making it unusable after testing.
Yes, the GLT-01 supports test methods for both material types, in line with ASTM F2096.
Pharmaceutical, medical device, food and beverage, and cosmetic industries all rely on gross leak detection to protect product integrity and meet regulatory standards.