Syringe Functionality Testing
In the pharmaceutical, medical device, and healthcare packaging industries, syringe functionality testing is a vital step in ensuring product safety, functionality, and regulatory compliance. Every component of a syringe—from the plunger to the needle and tip—must meet strict performance criteria defined by international standards such as ISO 11040-4, ISO 7886-1, and USP <1207>. At Ląstelių instrumentai, we specialize in providing reliable and customizable syringe functionality testing solutions that help manufacturers and quality control professionals validate syringe integrity and functionality with confidence.
Plunger Testing
The function of the plunger is central to syringe operation. One of the key tests evaluates glide force, which measures both the force needed to initiate movement (break-loose force) and the continuous force required to maintain steady motion along the barrel. If this force is too high, the syringe may be difficult to operate, leading to dosing errors. If it’s too low, the plunger may move unintentionally.
To conduct this test, the syringe is mounted horizontally and the plunger is pulled at a constant speed using a motorized fixture. The test system records force data in real time, producing a force-displacement curve that reveals variations or spikes that could indicate manufacturing flaws, lubrication issues, or component misalignment. Glide force testing helps ensure smooth delivery and user comfort.
Standartai: ISO 11040-4 Annex E, ISO 7886-1 Annex E, ISO 8537 Annex C, ISO 11499, ISO 11608-3

Barrel and Flange Testing
1. Flange Breakage Resistance
A vertical force is applied to the flange using a compression fixture until the flange fails. The force at break is recorded. To ensure the flange can withstand axial force without cracking or breaking during use.
Standartinis: ISO 11040-4 Annex C1
2. Front End Breakage Resistance
Through the probe applies force to the syringe tip until deformation or breakage occurs. This ensures the barrel won’t fracture under load—especially important in high-pressure applications like prefilled or injection systems.
Standartinis: ISO 11040-4 Annex C2
3. Dead Space Measurement
Dead space is the volume of fluid that remains in the barrel after full depression of the plunger. Excess dead space can result in wasted medication or inaccurate dosing. Measured by filling the syringe to a known volume, depressing the plunger, and calculating the residual fluid either by weight or volume.
Standartai: ISO 7886-1 Annex C, ISO 8537 Annex E
4. Graduation Marking Accuracy
It ensures dose markings are positioned and printed accurately for precise volume control. Using calibrated optical system or manual gauge compares printed lines with reference values.
Needle Testing
1. Needle Bond Strength
The needle is pulled vertically by a tensile tester until detachment. The peak force is recorded. To verify that the needle remains firmly attached to the syringe hub during use. The measured force must meet or exceed threshold values defined by ISO standards, ensuring the needle won’t detach during injection.
Standartai: ISO 11040-4 Annex G1, ISO 7864 Annex E, ISO 11608-2 Annex B
To assess the sharpness and ease of penetration into a standardized medium, simulating skin or tissue. The needle is driven into a synthetic elastomer or rubber substrate that simulates human skin. The maximum force required for entry reflects the needle’s sharpness. A sharper needle typically requires less force, reducing pain and tissue damage.
Standartai: ISO 11040-4 Annex F, ISO 7864 Annex D
To evaluate resistance to bending, ensuring the needle does not deform under normal handling. The needle is subjected to lateral force and deflection is measured.
Standartinis: ISO 9626 Annex B
To check needle durability and ensure safety during usage. The needle is bent to a specified angle and subjected to repeated stress cycles to test its mechanical durability.
Standartinis: ISO 9626 Annex C
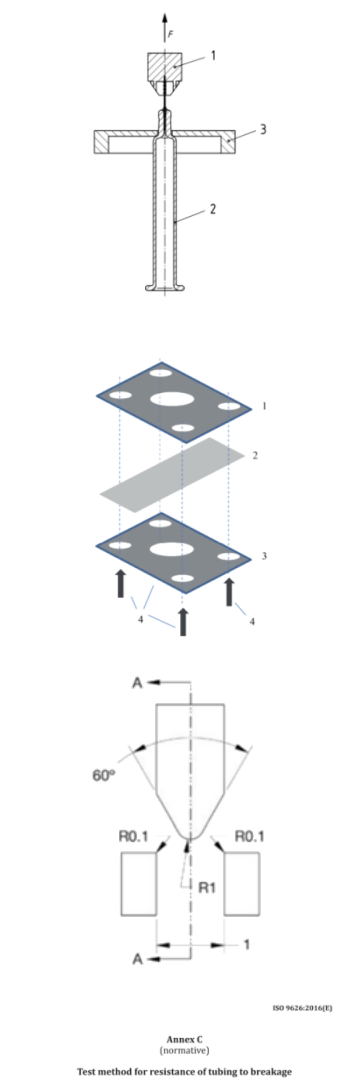
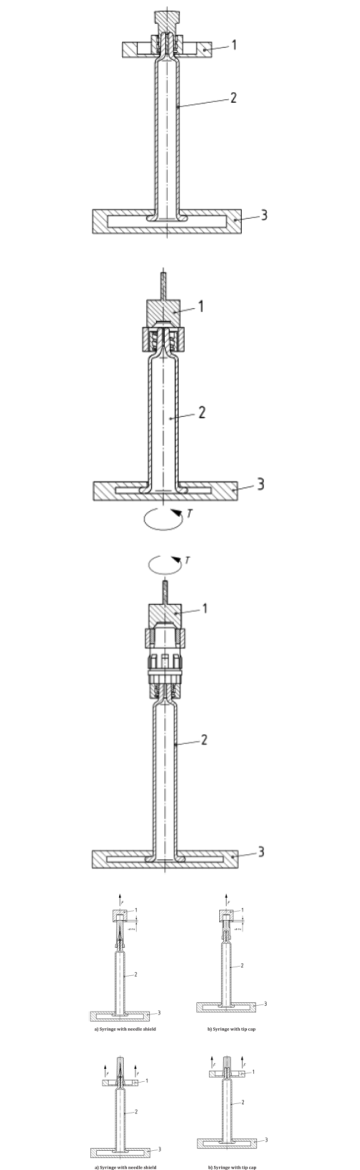
Tip and Luer Lock Interface Testing
1. LLA Collar Pull-Off Force
The syringe tip and any attached Luer lock components must ensure a leak-free and secure connection to other medical devices. One key test measures the pull-off force of the collar around the Luer lock. If this component detaches too easily, it could result in leakage or disconnection during critical procedures. Using the tensile tester, pull the collar axially until it detaches.
Standartinis: ISO 11040-4 Annex G3
2. LLA Collar Torque Resistance
The torque resistance of the Luer collar is evaluated to ensure that it does not rotate or unscrew under typical handling forces. In this test, a rotational load is applied, and the system monitors whether the collar withstands twisting without failure.
Standartinis: ISO 11040-4 Annex G4
3. Rigid Tip Cap Unscrewing Torque
It can evaluate the force required to unscrew the tip cap, ensuring it’s secure but not overly tight. This test involves rotating the tip cap by a motor or manually using a torque wrench to simulate opening, ensuring that it can be removed by medical personnel without excessive effort, yet still remain sealed during shipping and storage.
Standartinis: ISO 11040-4 Annex G5
4. Pull-Off Force of Tip Cap or Needle Shield
The tip cap or needle shield must also remain secure during storage but be removable with moderate force when in use. A pull-off test is performed by applying axial force at a controlled rate, measuring the peak force required for removal. Excessive force may hinder usability, while insufficient resistance could compromise sterility.
Standartinis: ISO 11040-4 Annex G6
Syringe System Integrity Testing
Air leakage testing evaluates the syringe’s ability to contain pressure without allowing gas exchange. The syringe is filled with air, sealed, and monitored for pressure decay. Any drop in pressure indicates the presence of a leak, which could compromise dosage accuracy or sterility.
Standartai: ISO 7886-1 Annex B, ISO 8537 Annex B
The syringe is filled with a dyed liquid, and internal pressure is applied. External surfaces are then inspected for any signs of leakage. This simulates the syringe’s ability to maintain its seal when filled with medication under stress.
Standartai: ISO 7886-1 Annex D, ISO 11040-4 Annex G2, ISO 8537 Annex F
For prefilled syringes and drug delivery systems, more advanced methods like container closure integrity testing (CCIT) are necessary to confirm microbial barrier effectiveness. Following USP <1207>, these tests can include vacuum decay, tracer gas detection, and high-voltage leak detection, each suited to specific syringe formats and regulatory requirements.
Standartai: USP <1207>, ISO 11040-4
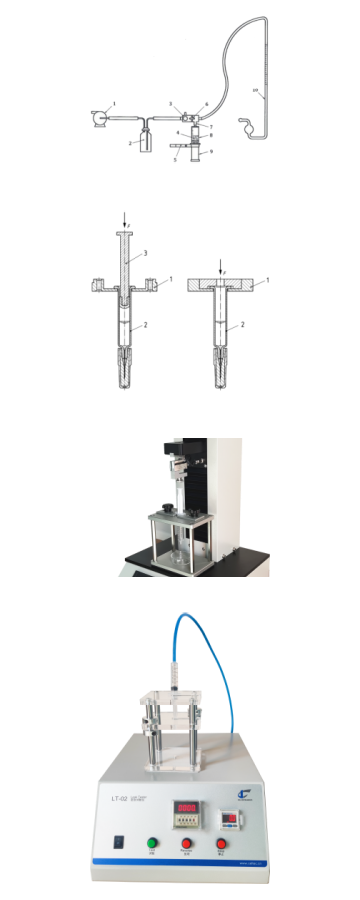
Talk to us
We understand the complexities involved in syringe production and testing, and we offer more than machines—we offer partnerships in quality assurance.